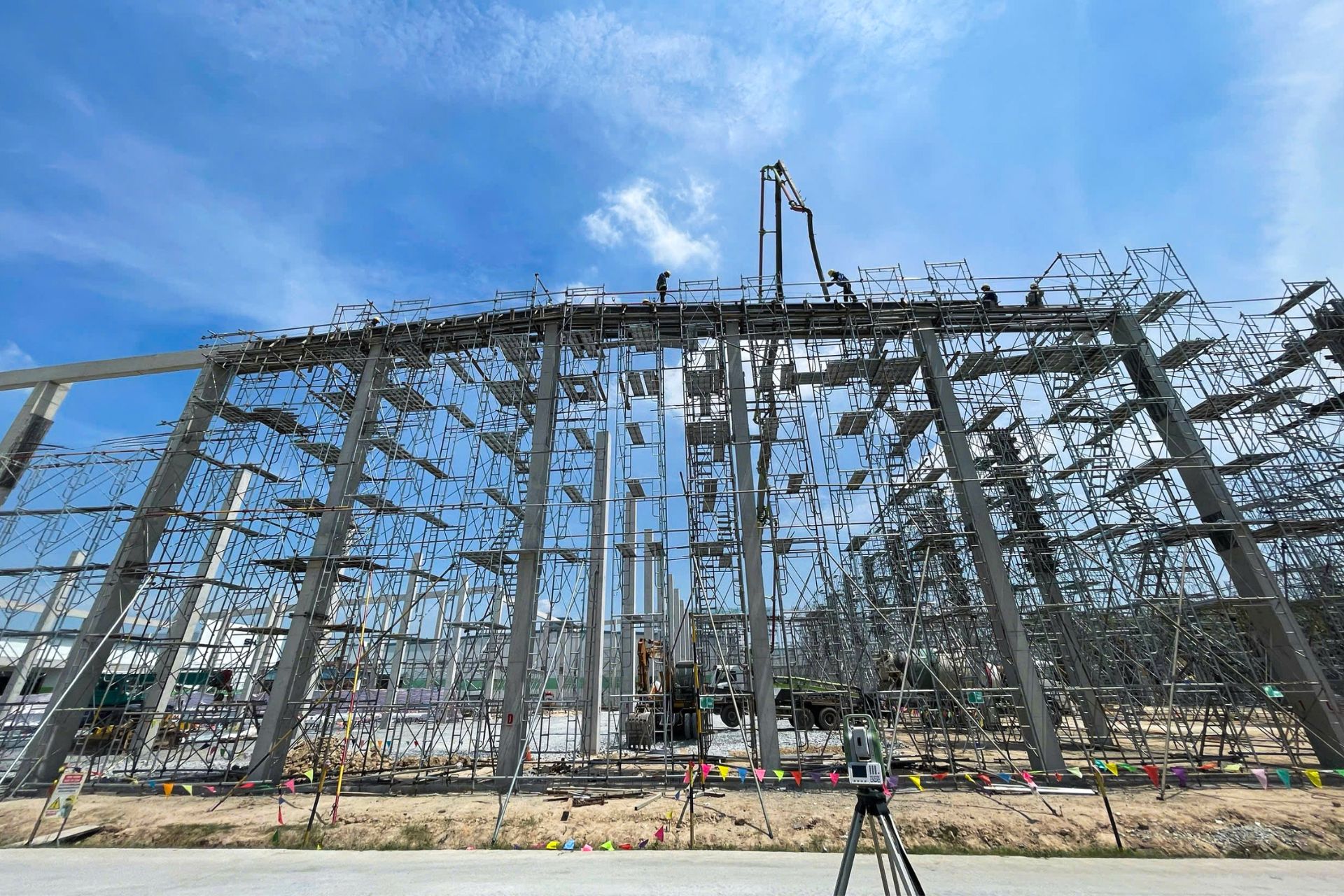
Professional and Reliable Industrial Factory Construction Services in Binh Duong
Industrial factory construction must meet multiple structural, technical, safety, and high-quality standards. A professionally built factory optimizes production, ensures worker safety, and enhances the longevity of the structure. In this article, TECO will provide a comprehensive overview of the professional industrial factory construction process and highlight the Showa Gloves factory project in Binh Duong.
Industrial Factory Construction Process
1. Site Survey and Project Planning
Conducting a thorough site survey ensures a stable and strong foundation. This process includes the following steps:
Geological and Soil Condition Assessment: The construction team will conduct exploratory drilling, soil sampling, and analysis of key indicators such as density, moisture, permeability, and subsidence. Determining the soil’s load-bearing capacity is crucial for selecting an appropriate foundation type. Geological assessments help identify potential risks like soil settlement, landslides, underground rocks, or other foundation-related issues.
Wind and Sunlight Orientation Analysis: Measuring wind direction aids in designing an effective ventilation system, while analyzing sunlight exposure ensures proper placement of windows, shading systems, and roofing structures.
Water Supply, Drainage, and Internal Traffic Evaluation: Assessing water supply infrastructure guarantees sufficient availability for production and fire prevention. Drainage systems are designed to prevent flooding during the rainy season. Internal traffic layouts must support smooth and efficient transportation within the factory premises.
2. Technical Drawing and Design
The technical design phase consists of:
- Architectural Design: Space planning to optimize functionality and operational efficiency. Key areas include production zones, warehouses, offices, canteens, parking lots, security stations, internal roads, and emergency exits.
- Structural Design: Based on soil surveys and load requirements, the foundation type is selected to ensure durability. Structural blueprints define the construction materials for columns, beams, and trusses—whether steel or reinforced concrete—to guarantee load-bearing capacity.
- Electrical, Plumbing, and Fire Protection System Design: The electrical system is designed to handle the factory’s power consumption while preventing overloads and electrical hazards. Plumbing systems must provide adequate water supply for production, domestic use, and fire safety. Fire protection systems include extinguishers, automatic sprinklers, emergency exits, and alarm systems to ensure workplace safety.
3. Construction Permit Application
Once the survey and design phases are complete, and all legal documentation is prepared, the contractor or investor must obtain a construction permit. Simultaneously, the investor proceeds with contractor selection, supervision consultancy, and project management based on their capabilities and requirements.
4. Foundation and Groundwork Construction
A robust foundation ensures the factory’s longevity and safety. A well-constructed foundation reduces risks, optimizes operational costs, and extends the building’s lifespan.
4.1 Site Preparation
Before foundation construction, the site must be cleared, obstructions removed, and the ground treated if necessary. The land is then leveled to the required elevation, ensuring a flat and stable surface.
4.2 Foundation Construction
Depending on soil conditions and structural loads, appropriate foundation types such as isolated footings, strip foundations, or pile foundations are chosen. Concrete and reinforcing steel quality is thoroughly inspected before pouring the foundation, following technical standards to ensure structural integrity.
Industrial factory foundation construction
4.3 Factory Floor Construction
The factory floor is reinforced concrete, designed for high durability and load-bearing capacity. The ground is compacted, waterproofed, and reinforced to prevent cracking, ensuring long-term stability.
Concrete pouring work for the super-flat foundation system of the factory.
5. Structural Construction
The two most common structural types for industrial factories are pre-engineered steel frames and reinforced concrete (cast-in-place or precast concrete). Pre-engineered steel structures are ideal for projects requiring rapid construction, flexibility, and large open spaces. Reinforced concrete structures offer superior durability and load-bearing capacity. Steel components are prefabricated and assembled on-site, whereas reinforced concrete elements may be cast in place or pre-manufactured.
TECO constructs precast concrete components of SMC Long Duc project.
Next, the roof trusses and purlins are installed to reinforce the factory’s structural framework, ensuring load-bearing capacity and stability. After completing the frame, the roofing and exterior wall finishing process is carried out. Corrugated metal sheets or insulation materials are used for roofing to reduce the internal temperature of the factory and enhance the building’s durability.
6. Installation of Factory Technical Systems
This phase includes the following:
Electrical System: Installation follows the design blueprint to ensure safety and efficiency. It includes lighting, electrical panels, and industrial machinery connections. Final inspections confirm operational stability and compliance.
Plumbing and Drainage System: Piping systems are installed according to industry standards to ensure smooth water supply and wastewater drainage, preventing leaks and blockages.
Fire Protection System: Compliance with fire safety regulations involves installing fire extinguishers, automatic sprinklers, and smoke detectors. Regular inspections ensure full functionality and adherence to safety protocols.
Equipment Installation and Technology Setup: Industrial machinery and systems are installed according to the design plan, ensuring they meet technical specifications and operational demands.
7. Surface Finishing, Inspection, and Project Handover
After completing structural and system installations, finishing work enhances the factory’s aesthetics. Walls are painted, and floors may be coated with epoxy for durability, slip resistance, and heavy load tolerance.
Before handover, the entire project undergoes rigorous inspections to ensure compliance with construction standards. The acceptance process covers foundations, structural framework, technical systems, and finishing touches. Fire protection systems are also thoroughly examined.
Once the investor approves the final inspection, the project is officially handed over, including complete technical documentation and operational guidelines. At this point, the factory is ready for full-scale production and operation.
Key Construction Standards for Industrial Factories
Solid Foundation
The foundation is a crucial factor determining the durability of the entire building. If the soil is weak, appropriate measures such as piling, concrete pile pressing, or soil improvement through compaction and cement grout injection should be applied to enhance load-bearing capacity. The foundation construction must meet technical and quality standards to prevent subsidence and ensure the building’s longevity.
High-Quality Structural Integrity
The structural system, including columns and trusses, must withstand environmental impacts. Additionally, the roofing and surrounding walls should utilize insulating, soundproof, and waterproof materials to protect against external conditions.
Construction Materials Meeting Strict Quality Standards
All construction materials must have a clear origin and comply with strict quality standards. From concrete, cement, and structural steel to connecting bolts, wall and roof materials, and paint, everything must ensure high durability, safety, and quality.
Construction materials must meet quality standards.
Safe Construction Practices
Workers must be equipped with full protective gear and trained in occupational safety, working at heights, and operating machinery and equipment. During the factory’s operation and production phases, safety equipment, fire prevention systems, and hazard warning signs must always be in place to ensure workplace safety.
Technical Systems Meeting Quality Standards
To ensure safety, efficiency, and legal compliance, the contractor, investor, and related parties must thoroughly inspect the electrical system, water supply and drainage, ventilation and cooling, and fire prevention systems. After the inspection, a detailed handover report should be prepared, and operational training should be provided to employees to ensure long-term, safe, and effective use.
Environmental Protection Infrastructure
Environmental regulations are mandatory in industrial construction. Rainwater drainage, wastewater collection and treatment systems must comply with environmental protection standards. Additionally, noise and vibration control measures must be implemented during machinery operation to minimize impact on surrounding areas
Showa Gloves Factory Construction Project in Binh Duong
- Investor: Showa Gloves Vietnam
- Project Type: Industrial Factory
- Scope of Work: Structural Construction
- Scale: 1 hectare
- Status: Under Construction
- Location: VSIP 1 Industrial Park, Thuan An, Binh Duong
TECO serves as the contractor for the construction of the Showa Gloves factory. The factory is located in VSIP 1 Industrial Park in Bình Dương, focusing on structural works. TECO is responsible for the foundation and flooring construction, ensuring a solid and stable structure for the project. After completing the foundation, the process continues with the installation of reinforcement, followed by the construction of columns, beams, and floors, meeting load-bearing and long-term durability requirements. The entire construction process is carried out according to technical and safety standards, ensuring project quality and progress as required by the investor.
Actual image of the factory construction in Binh Duong.
Actual image of the factory construction in Binh Duong.
Actual image of the factory construction in Binh Duong.
Actual image of the factory construction in Binh Duong.
Actual image of the factory construction in Binh Duong.
Actual image of the factory construction in Binh Duong.
Conclusion
Industrial factory construction requires seamless coordination across multiple phases—from surveying, designing, and permitting to execution and finishing. Each step plays a crucial role in ensuring structural quality, safety, and longevity. TECO hopes this article provides valuable insights into the complete construction process and the essential standards to follow, helping investors select a reliable contractor for their projects
- Head Office: 39 Nguyen Trung Ngan, Ben Nghe Ward, District 1, Ho Chi Minh City
- Representative Office: No. 85, Street 19, An Phu Ward, Thu Duc City
- Email: teco@tecoarch.com
- Hotline: 02866 596 979 – 0911 111 929