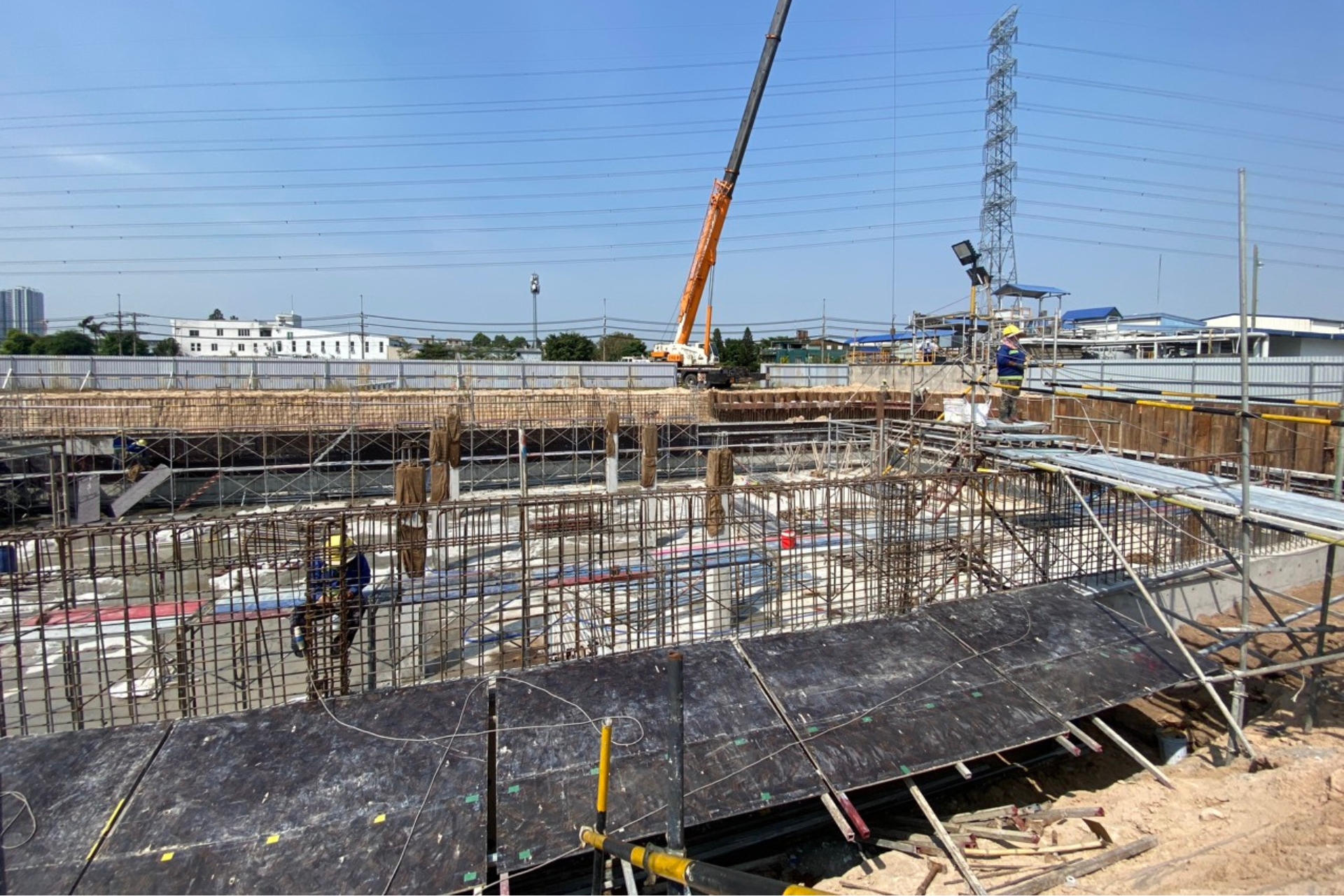
Key Factors Determining the Cost of Factory Construction
Factory construction is a crucial investment item in the manufacturing industry, directly impacting a business’s operational capacity, efficiency, and expansion strategy. However, to develop accurate cost estimates and effectively manage budgets, investors must clearly understand the key factors influencing factory construction costs. In the article below, let’s explore with TECO the critical elements that determine factory construction expenses.
Key factor determining the cost of factory construction
Key Factors Affecting Industrial Factory Construction Costs
1. Scale and Functionality of the Factory
Project scale is the foremost and most significant factor directly influencing the total cost of factory construction. The construction area, number of floors, building height, and the number of functional areas (production facility, warehouse, office, technical zones, etc.) will determine:
-
The quantity of materials required
-
Number of workers and construction duration
-
Requirements for structural load-bearing, flooring, and foundations
-
Investment level in auxiliary systems (fire protection, electrical–water systems, ventilation, environmental treatment, etc.)
Note: A factory with the same floor area but requiring GMP, HACCP standards, or special conditions for temperature and humidity will cost significantly more than a standard factory.
The scale of the project directly impacts the total construction cost.
2. Structure and Building Materials
Construction costs are heavily influenced by the structural solutions chosen by the investor and the design unit. Key elements include:
Foundation Types
-
Types such as isolated footings, strip foundations, or pile foundations are selected depending on site geology.
-
Weak soil areas require complex foundation treatment, which increases costs.
Structural Frame System
-
Factories using pre-engineered steel frames generally cost less than those using reinforced concrete structures.
-
However, factories requiring soundproofing, thermal insulation, or fire resistance may need special structural combinations, increasing costs.
Finishing Materials
Materials typically account for 40–60% of total construction costs. Depending on durability, load-bearing requirements, and aesthetics, businesses can choose from:
-
Steel frames: Pre-engineered steel is widely used due to high durability and quick installation. Steel prices vary based on thickness and type (H-beam, I-beam, U-beam, etc.).
-
Roofing: Options include cold corrugated iron, insulated panels, or composite panels. Thicker materials are more expensive but have a longer lifespan.
-
Factory flooring: Reinforced concrete is standard for heavy-load areas.
-
Auxiliary materials: Roller doors, windows, drainage systems, and anti-rust paint also impact total costs.
At TECO, we always advise clients to select materials based on sustainability, cost-effectiveness, and ease of maintenance—instead of just initial price—because we prioritize construction quality above all.
3. Construction Site and Conditions
The location of the construction site significantly affects many cost-related variables:
-
Transportation distance for materials and equipment
-
Accessibility for construction vehicles and machinery
-
Weather conditions: Areas with heavy rain, flooding, or mountainous terrain impact foundation work and project timelines
-
Legal requirements: Some industrial zones or provinces have specific regulations on construction, fire safety, or environmental protection, which can lead to additional costs.
TECO is currently implementing the SMC Long Đức Factory Project in Đồng Nai.
4. Technical & Technological Systems
A modern factory cannot operate without auxiliary systems such as:
-
Electrical systems (lighting, production power supply)
-
HVAC (Heating, Ventilation, and Air Conditioning)
-
Water supply and drainage systems
-
Standard-compliant fire protection systems
-
Wastewater, dust, and toxic gas treatment systems (if applicable)
Costs for these systems depend on production scale, industry requirements, and level of automation.
In addition, smart technologies such as BMS (Building Management Systems) and IoT for production monitoring may increase initial investment but offer long-term operational savings.
Fire protection systems are mandatory for industrial factories.
5. Labor Costs and Construction Timing
Factory construction costs are also impacted by:
-
Regional labor rates (e.g., HCMC, Bình Dương, Long An typically cost more than central provinces)
-
Construction season (peak seasons drive up labor and material prices)
-
Market trends for materials (affected by the price of steel, cement, fuel, etc.)
Note: Investors should plan construction during periods of stable material prices and avoid peak seasons like year-end or post-Tet to optimize costs.
6. Timeline Requirements
Industrial factory construction typically lasts 3–6 months. However, if the project involves an expansion or renovation within an operational factory, construction may need to be completed much faster and without disrupting production. This requires:
-
Increased manpower
-
Nighttime construction
-
Well-prepared machinery, labor, and construction methods
These demands inevitably drive up construction costs compared to normal conditions.
Choosing the Right Contractor to Optimize Construction Costs
Selecting the right contractor not only determines construction quality but also plays a vital role in optimizing overall costs. An experienced contractor understands each construction phase—from structural design to material selection and construction management—helping avoid waste and reduce unnecessary expenses. They can also recommend technical solutions to shorten timelines and efficiently utilize available resources. Additionally, reputable contractors often have relationships with material suppliers, allowing for better price negotiations without sacrificing quality.
With TECO, a trusted contractor in industrial construction, we are committed to supporting businesses from planning to handover, ensuring reasonable, transparent, and optimized investment costs.
Conclusion
Building a factory is more than just erecting a structure of concrete and steel. It is a large, long-term investment that demands precise calculations. With years of experience in industrial construction, TECO is committed to delivering optimal, cost-effective, and efficient factory construction solutions for all businesses.
Contact us today for a free consultation and customized quote that suits your specific needs.
TECO Architecture & Construction Joint Stock Company – Where Life Value Is Built
-
Head Office: 39 Nguyễn Trung Ngạn, Bến Nghé Ward, District 1, HCMC
-
Representative Office: 85, Street No. 19, An Phú Ward, Thủ Đức City
-
Email: teco@tecoarch.com
-
Hotline: 02866 596 979 – 0911 111 929